What can you expect from streamlining processes using the Lean Six Sigma method?
“The Six Sigma approach to process improvement is based on the idea that all processes, from design through production to customer services, exhibit certain variations. These variations can lead to product defects, which cost us time and money.”
“The variations in processes can be reduced through various methods, from more intuitive management improvement techniques to more complex methods like Design of Experiments (DOE). They all share the common principle of systematically identifying and eliminating the root causes of problems. By reducing the variability of the process, the number of defective products and reworks (uncontrolled incidents in service processes) decreases. To prevent the process from reverting to its original state, standardization is subsequently ensured.”
img.1 Variability (Sigma) and number of errors (DPMO)
img.2 Variability (Sigma) and losses in processes
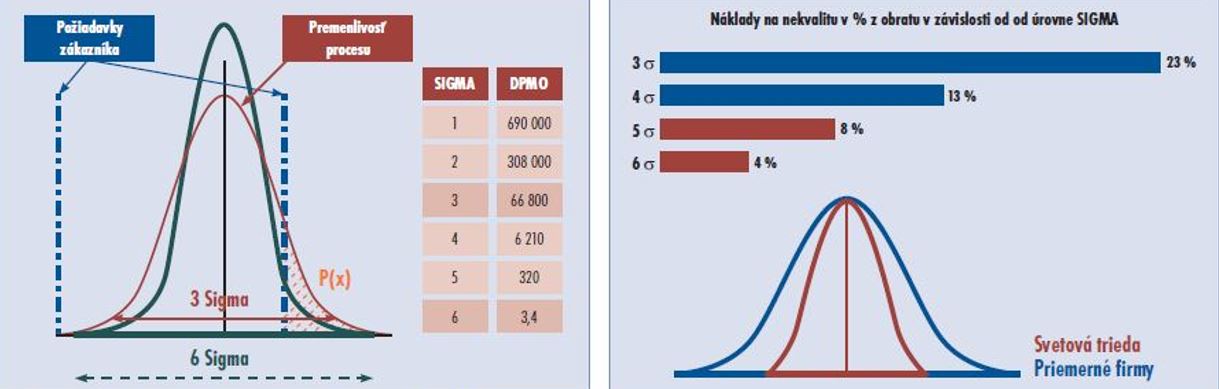
“Experiences from our consulting practice show that processes in manufacturing companies in the automotive industry, which already have a quality assurance system in place, typically operate at a level of around 3.5 to 4 SIGMA, and in some processes even higher. In such cases, improving the company’s processes by 0.2 SIGMA translates to economic benefits of around 1% of the company’s revenue. Therefore, if successful applications in companies where Six Sigma is already implemented can be approximated, and the overall direct and indirect costs usually remain below 25% of the improvement benefits (in some cases only 10%), implementing SIX SIGMA represents a high-return investment.”
img.3 Example of benefits from Six Sigma projects in the first year of training and project coaching by FBE lecturers in a large manufacturing company
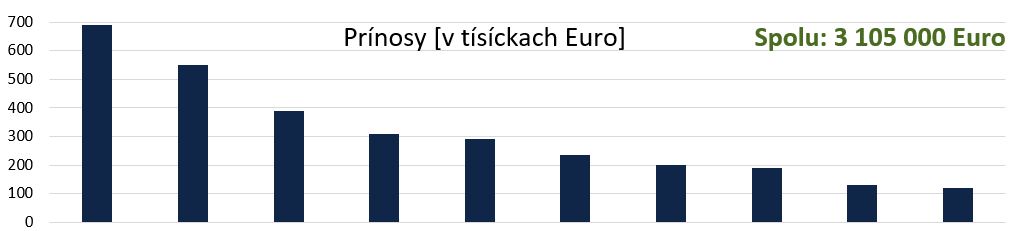
PREPARATION OF “KEY PLAYERS”
“A typical implementation of Lean Six Sigma begins with the leadership team, although sometimes we return to this step only after training project leaders. During workshops, the leadership collaborates and approves the implementation of the Lean Six Sigma program after thorough discussions. Subsequently, individuals are trained in the Lean Six Sigma methodology, including project leaders known as ‘Black Belts,’ and key team members and solvers of smaller projects known as ‘Green Belts.'”
“After some time, experienced ‘Black Belts’ can progress to become ‘Master Black Belts’ after further training, taking on the role of a coach. The number of Green and Black Belts is determined by the organization based on its needs. Successful completion of the Lean Six Sigma training for Black Belts also requires the completion of an actual project. The training includes an analysis of the measurement system, the use of Design of Experiments (DOE), and graphical methods of process analysis, including Statistical Process Control (SPC).”
IS SIX SIGMA SUITABLE FOR MANUFACTURING AS WELL AS FOR SERVICES?
“Our consultants often utilize typical Six Sigma improvement approaches through the DMAIC methodology, often in combination with best practices from services. An example of this is the use of ITIL procedures for data management within incident management. The table in image 4 provides an example of the integration between the DMAIC project cycle and ITIL elements. The Six Sigma process improvement methodology provides guidance on measuring process quality and enhancing their performance. This complements what is lacking in ITIL, a collection of best practices, which is the guidance on implementing a Service Improvement Program (SIP).”
img.4 Six Sigma project phases and elements of service management (example from IT Service Management)
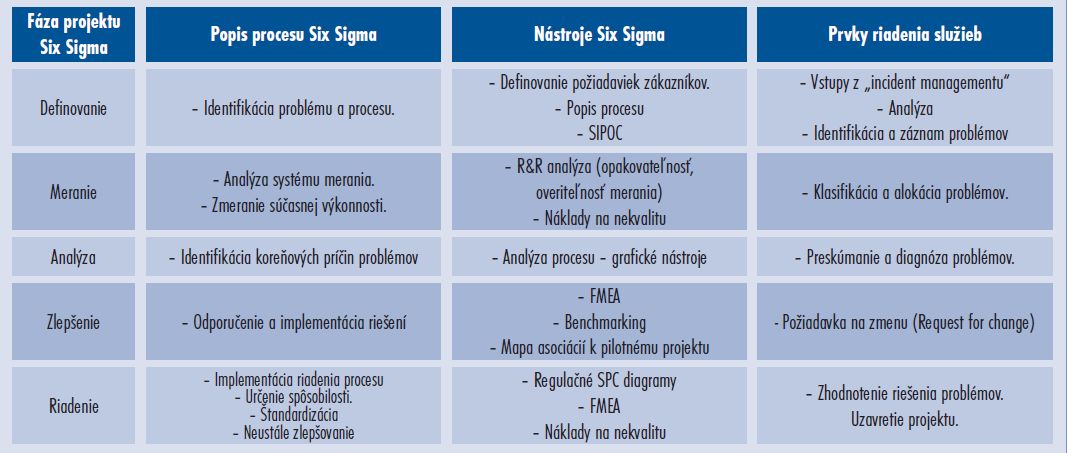