CP and CPK: Key Indicators in Statistical Process Control
In statistical process control (SPC), CP and CPK play a key role in measuring and evaluating process stability and capacity. Understanding and interpreting these indices enables companies to identify and resolve problems in processes, thereby improving product and service quality, reducing costs, and increasing customer satisfaction.
What is CP?
CP (Control Process) is an index that expresses the degree of control over a process. It is calculated as the ratio of the average value of the process to the width of the control limit. The ideal CP value is between 1 and 2, indicating a stable process with results within the desired limits.
CP values and their interpretation
- CP < 1: The process is not under control, the results are variable and require correction.
- 1 ≤ CP ≤ 2: The process is under control but approaching the control limit. It is recommended to re-evaluate the process and optimize its parameters.
- CP > 2: The process is under good control with stable results.
What is CPK?
CPK (Control Process Capability) assesses the capacity of a process to meet customer requirements. It is calculated as the ratio of the control limit width to the tolerance specified by the customer. A CPK > 1.33 indicates that the process is capable of meeting the requirements with a high degree of confidence.
CPK values and their interpretation
- CPK < 1: The process is not able to meet the customer’s requirements and modification is required.
- 1 ≤ CPK ≤ 1.33: The process is able to meet the requirements, but with a low level of certainty. Improvements to the stability and capacity of the process are recommended.
- CPK > 1.33: The process is highly capable of meeting customer requirements with a high degree of certainty.
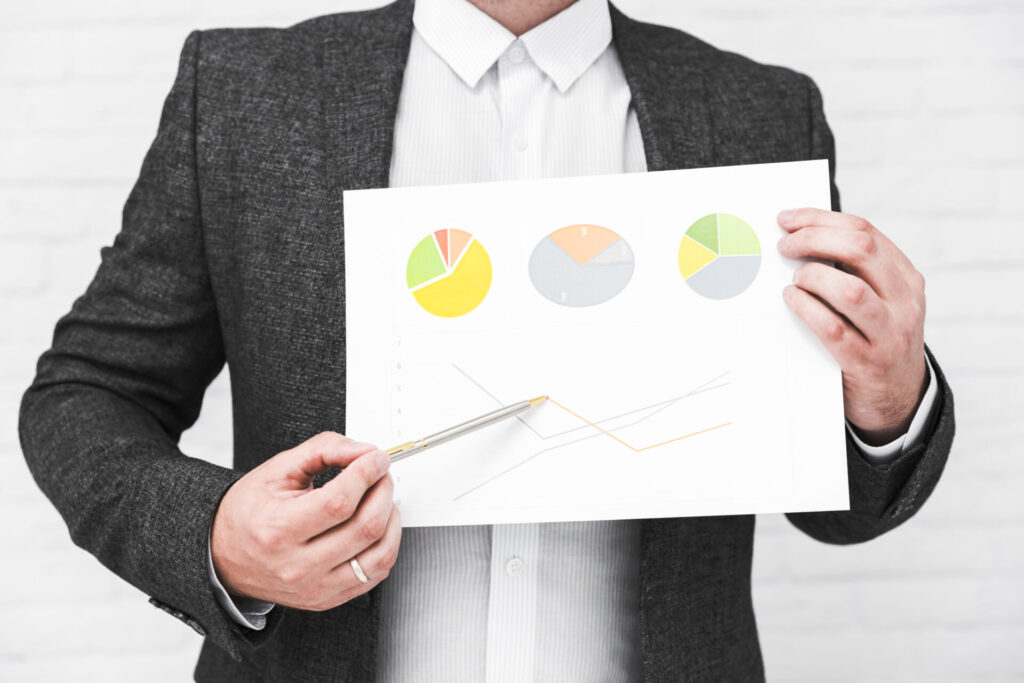
Improving CP and CPK
The implementation of various SPC tools and techniques enables effective improvement of CP and CPK. The most common include:
- Value Stream Mapping
- Cause and effect analysis (Ishikawa diagram)
- Process standardization
- Poka-Yoke (error prevention method)
- Six Sigma (a method aimed at eliminating variability and errors)
CP and CPK are valuable indicators in SPC that help firms:
- Improve process stability and capacity
- Reduce variability and error rates
- Improve product and service quality
- Reduce costs
- Improve customer satisfaction
By implementing CP and CPK in combination with appropriate SPC tools, companies move towards more efficient operations and continuous improvement. In the context of Six Sigma Black Belt certification, it is important to have a good understanding of these statistical indicators and to be able to interpret and use them correctly to improve processes and increase the quality of outputs.